CerarMix
Steel corrodes, cement crumbles; material deterioration due to harsh elements increases maintenance costs and production downtime.
Used either as a coating to repair existing infrastructure or in the manufacture of individual parts and components with superior physical attributes compared to competitive alternatives, CerarMix minimizes material degradation and infrastructure failure.
Flexible Ceramic Armor Coatings Provide Ultimate Protection
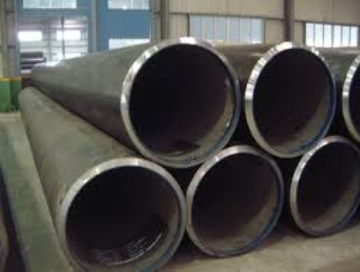
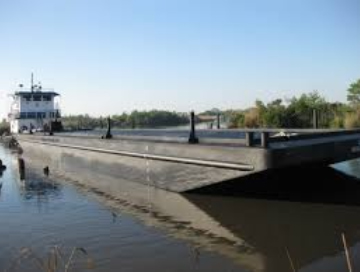

Announcing a revolutionary new product and process which is changing the face of the industrial coating industry. CerarMix Coating Systems provide solutions that help manufacturers worldwide to increase productivity, lower material costs and improve finished substrate and part quality.
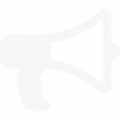
Announcing a revolutionary new product and process which is changing the face of the industrial coating industry.
Announcing a revolutionary new product and process which is changing the face of the industrial coating industry. CerarMix Coating Systems provide solutions that help manufacturers worldwide to increase productivity, lower material costs and improve finished substrate and part quality.
What makes CerarMix standout?
◈ CerarMix Defined
CerarMix is an industrial strength, high performance adherent which forms a dense, inert layer of protective, armor-like, ceramic-metallic-polymer coating.
CerarMix is impervious to both oxygen and moisture.
CerarMix acts as a primer for bare substrates and a topcoat -- combining strength and durability in a lightweight material.
CerarMix is formulated using a patented nanotechnology which substantially improves durability and performance, thus extending the life of any existing substrate subject to impact by corrosion, erosion or heat while increasing production and substantially reducing repair and maintenance costs.
CerarMix Coating Systems have no VOCs (Volatile Organic Compounds), no HAPs (Hazardous Air Pollutants), no flash point, and no hazardous disposal issues.
◈ Application/Uses
CerarMix is the gold standard for the coating industry -- providing solutions to the world's most important manufacturing and processing environments for over 20 years.
CerarMix has performed successfully in over 1,000 proprietary knowledge-based coatings solutions used in a wide-range of industrial, military, and OEM applications.
CerarMix chemically bonds to substrates at the molecular level using nanotechnology. Applied using the patented CerarSpray system, CerarMix can be tinted to achieve virtually any color pigmentation with finishes ranging from textured, low-gloss or matte, to high-gloss.
CerarMix Coating Systems have no VOCs (Volatile Organic Compounds), no HAPs (Hazardous Air Pollutants), no flash point, and no hazardous disposal issues.
◈ Functionality
CerarMix performs at its highest level in environments that are corrosive, abrasive, erosive and/or affected by fire, heat and chemical attack. CerarMix withstands long periods of immersion in liquids including aggressive solvents and other chemicals.
As a fire retardant with 0% flame spread, CerarMix Coating Systems give the added benefits of stain and mold resistance. Capable of withstanding steam and high pressure cleaning, CerarMix is non-toxic, environmentally friendly, fast curing offering a high coverage rate for single-coat applications.
CerarMix creates a "forever" bond with the base material with coatings that do not chip, crack, flake, peel or fade. Combining properties that match ultra-hard diamond singularity.
CerarMix is engineered to provide unrivaled non-stick, corrosion and chemical resistance, as well as, low friction surface properties -- more than other composite coating systems available today.
CerarMix used as a thermal spray coating will withstand severe temperature extremes without any loss in physical properties. In addition to their high heat stability, CerarMix eliminates thermal transfer, is non-conductive and electrically insulating.
CerarMix
Specifications
Bond Strength: Concrete > 400 psi, (concrete fails before the bona), Steel 1,200 psi
Indentation: MIL-D-3 1 4 3 F (None)
Heat Resistance: 400°F Continuous, 600°F Transient
Flammability: UAB-DTRC-MIL-STD: 2031,
University of Alabama/Burn-Through Test-Military Standard -self-extinguishing after 30 min. exposure 800
Water Solubility: .0095
Coefficient of Thermal Expansion: 6.5 x 10-6
Hardness (Diamond = 10F): Moh: 9F
Polymer Hardness: Barcol:80
Compressive Strength: ASTMD-759: 16,000 psi
Tensile Strength: ASTMD-307: 9,500 psi
Flexural Strength: ASTMD-790: 21,300 psi
Modulus of Elasticity: ASTMD-790: 0.9 x 106
Abrasion Resistance: ASTMD-4060 CS-17 Wheel: 0.020g
Impingement Test: Negligible erosion loss and 40% improvement over 2205 Duplex Stainless Steel